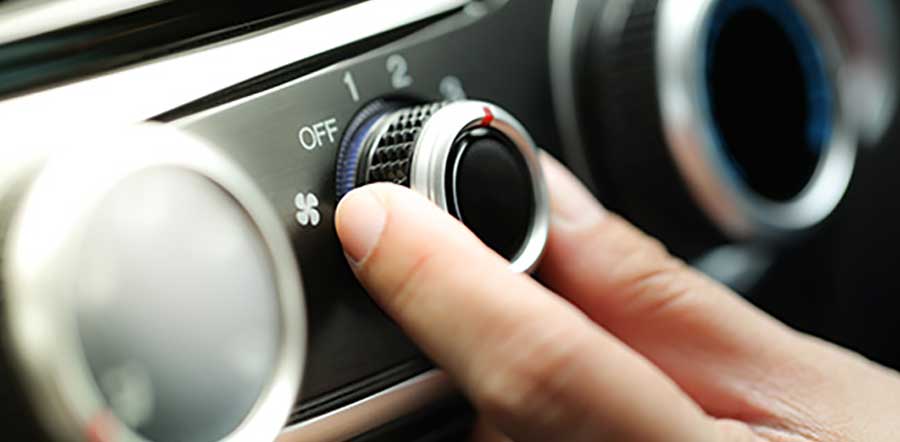
There is pressure to:
- Minimize development costs and time
- Noise and weight reductions
- Increase durability
- More and more stringent regulations to reduce CO2 emissions.
Pressure to minimize development costs and time
Development costs are rising significantly as designs are moving to larger-sized scroll and rotary compressors. Electric car batteries are big and heavy, and they make it incredibly difficult when attempting to find space and weight savings during the design process. Not only the thermal management of the cabin, from cooling to heating (the engine will not heat the cabin anymore) needs to be managed. Also, the cooling of the engine and the batteries require engineered solutions. Additionally, the batteries require either pre-heating or pre-cooling.
Compliance with increasingly more stringent regulations
The decarbonization of road transportis an essential target for :
- China: net-zero greenhouse gas emissions by 2060
- Europe: to reach zero-emission road mobility by 2035 (an EU fleet-wide target to reduce the emissions produced by new passenger cars and light vehicles by 100% compared to 2021).
- USA: President Biden recently announced a new target to achieve 50-52% reductions from 2005 levels in economy-wide net greenhouse gas pollution in 2030.
This puts pressure on design engineers to increase efficiency of their compressors by reducing weight and size, as well as optimizing friction management and consequently increasing durability of their compressor.
Noise reduction poses new challenges
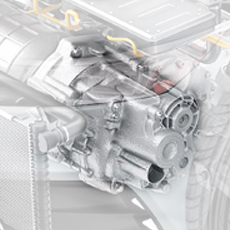
Nowadays, with the increase of electrified vehicles and overall noise reduction, the noise inside the car cabin is more and more related to embedded components. During the car development, also compressor suppliers are consequently asked by car manufacturers to reduce noise created by their compressor. Noise reduction has consequently become an important challenge in the design process of the compressor.
Avoid shaft seizure by heat controlling
The heat generation of the shaft is a critical point of any compressor. To prevent the risk of shaft seizure, the heat generation of the shaft must be controllable.
Global post-COVID supply chain disruptions
Multiple national lockdowns continue to slow or even temporarily stop the flow of raw materials and finished goods, disrupting manufacturing globally. In addition, many companies have laid off staff or lost employees due to COVID.
Manufacturing companies are nowadays forced to reconsider their supply chains and become more resilient, collaborative and networked with their suppliers and consider localizing their supply chain to a certain degree which will help them also to reduce their CO2 footprint.