This depends strongly on the application. Some applications require low friction (e.g. bearing materials) while others require high friction (e.g. brake systems). For most of the applications, minimum wear of the materials is a primary goal. For many applications, a defined sweet spot between low friction levels and good wear performance is often targeted.
When designing experiments describing friction and wear, tribological testing can be placed into one of six main categories, from field tests in Category I to simplest laboratory model tests Category VI.
Category I: A field trial is conducted under normal operating conditions, which may include extended operating conditions. This results in poor repeatability but is close to real world requirements the tribological system will face.
Category II: Experiments are undertaken with a complete piece of equipment in a plant environment. These experiments may achieve results close to normal operating conditions and can be conducted over a period of time to replicate extended operating conditions while limiting environmental impact.
Category III: Components, subsystems or assemblies are tested in a laboratory approximating normal extended operating conditions, yielding medium repeatability
Category IV: Laboratory testing is conducted on serial standard components using scaled down testing plant apparatus.
Category V: Experiments are conducted on a specimen with test equipment to deliver close to normal operating conditions with excellent repeatability.
Category VI: A bench test is conducted with simple laboratory test equipment.
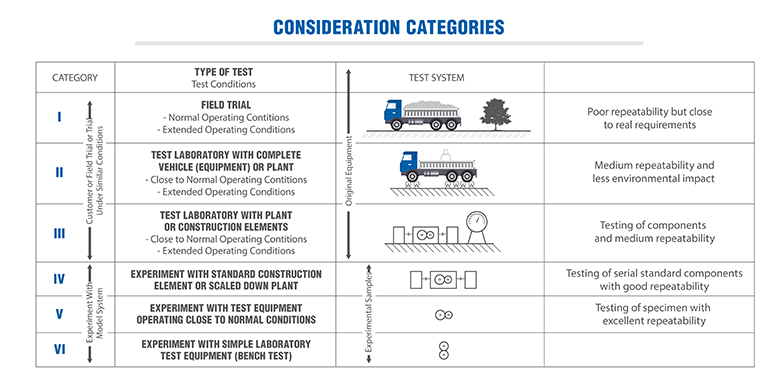
It is important to remember that in categories I through III, the system structure of the original tribo- aggregate remains consistent, and only the collective stress is simplified. Categories II and III offer more reproducible collective stresses than category I. In contrast, in categories IV through VI, the system structure is simplified with the disadvantage of decreasing predictability in the transferability of test results to comparable practical tribo-technical systems. Categories IV through VI offer better metrology of the sub tribo-contact, lower cost and a tighter testing timeframe.1 So with an ascending order of the test categories the test time as well as the test cost increases significantly, but transferability of the test result increases as well.
How can we apply the test categories to the sub tribo-system bearing?
Tribological testing of bearing materials can be divided into four main categories:
- Product performance descriptions, which would include categories IV and III to ensure the transferability of results.
- Production/Manufacturing monitoring, including categories VI through IV, with category III also being a possibility.
- Customer-related testing of bearings may include categories III through V, keeping in mind that category V is relevant only if the test can be adapted as close as possible to the application.
- All categories may be used to support material designers, with lower categories in the early stages of development for pre-selection and higher-numbered categories coming into play as the subcomponents and the final product are available.
1 Horst Czichos, Karl-Heinz Habig: Tribologie Handbuch: Tribometrie, Tribomaterialien, Tribotechnik, Vieweg+Teubner Verlag, 2010