GGB recently developed a new type of pintle bearing for refurbishment of the miter gates in the Panama Canal’s lock system. Among the requirements specified for the new hydro bearings were 25-year service life, abrasion-resistance, underwater operability and ease of assembly and operation.
In addition the U.S. Army Corps of Engineers stipulated the use of self-lubricating instead of greased bronze bearings to eliminate contamination of the water.
ADVANCED POLYMER RESIN
GGB had to submit certified, third-party test results to have its bearings considered for the project. After correlating the specified needs with the functional requirements of the bearings and extensive study of various materials, the company selected an advanced polymer resin with PTFE fibers.
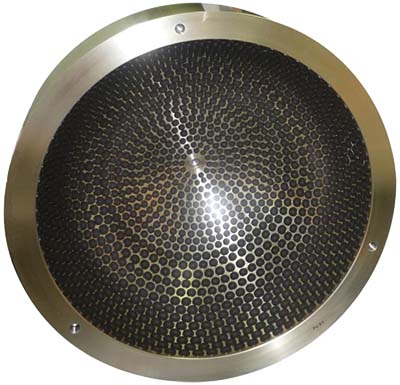
GGB developed a GGB-DB® cast bronze hemispherical bearing lined with the new material in the form of embedded, solid lubricant plugs protruding above and covering 70% of the surface area.
This configuration not only allowed for efficient flushing of the bearing via integral cleaning grooves, but also enhanced its structural integrity and facilitated its production.
PROTOTYPES FOR TESTING
Quarter-scale prototypes were submitted to Powertech Labs for testing, which yielded excellent results in terms of static/dynamic friction, axial/horizontal direct wear and temperature resistance.
Full-size bearings were then produced for finite element analysis, which confirmed that contact pressure and shear force were well within their mechanical properties with a sufficient margin of safety.
In addition to hydropower applications, the new bearings are also suitable for use in bridges, telescopes and other applications involving pivoting movements and requiring high axial load resistance.